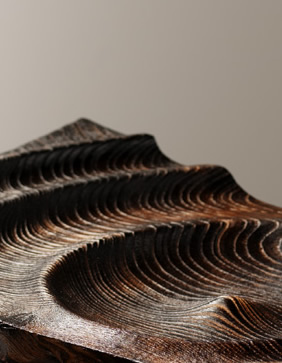 |
|
Techniques and Finishes
Turning and carving
All the wood I use is locally sourced, i.e. it comes from farms, gardens and local forests, it is almost always from windblown trees or trees that have had to be removed because they are dead, dangerous of have been cleared for new roads and houses etc.
When the wood arrives at my workshop it is still fresh, wet and in the round. I usually leave the logs lying outside to age and spalt. Spalted wood has been attacked by fungus and often has spectacular colouring with distinctive black lines running through it, when the wood is dry the spalting is stable and will not change or fade with sunlight.
When I feel the time is right to use the wood I rough it into shape with a chainsaw before mounting it on my lathe for turning. As the wood for large vessels is wet and can weigh hundreds of kilos it can take several hours to get a large piece of wood into my workshop and mounted safely on the lathe. To turn large work I have had to adapt and make my own specialised tools, these are all hand held and can be up to five feet long.
All my work is started as wet wood, some is partially turned, then kiln dried for several months before being remounted and turned to completion. Larger work, natural edged bowls and vases are often turned to completion from wet wood then left to dry before being polishing off the lathe. All wet turned work will have shrunk during drying and is sometimes slightly oval or wrinkled. Both these ways of working eliminate the natural tensions in wood that can cause splits and cracking, this makes my finished work both flexible and stable, allowing it to cope with changes in humidity from Summer to Winter as well as stress from central heating and direct sunlight etc.
Some parts of my work is black and textured this is generally achieved with a gas blow torch or pyrography machine, after burning it is wire brushed and cut back to reveal the unburnt wood underneath.
Finishes
If its a bowl and you can put something in it like fruit, it's nearly always finished with Rustins Danish Oil, this is a food safe waterproof finish that has been applied to the bare wood and built up in layers over several days. Danish Oil can be reapplied as and when needed, (I have not had to re-oil a bowl in the last twelve years) you can clean work like this with a damp cloth.
If it is a vase it will usually have a paste wax polish on it, I use Liberton Black Bison, Neutral Wax, this is a high gloss finish which shouldnĂt need any further treatments unless it gets wet, water will dull the surface polish and make it opaque but will not effect the wood underneath. If this happens all that is needed to bring back the shine is a good rub with a duster, cloth or kitchen roll, if this doesn't work a further coat of good quality wax polish will do the job.
|